top of page

Construction Sector
Washing systems for cement mixer and tanks at concrete batching plants
Underlying Issues with Cement Mixers; the presence of leftover cement in the mixer after the mixing process.
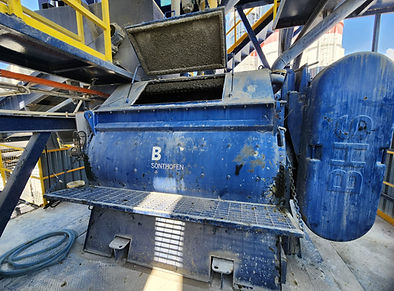
The accumulation of leftover cement in the mixer poses several challenges for our customers. This issue can lead to inefficiencies, increased cleaning time, and potential material waste, which can affect overall project timelines and costs
Accumulated residual cement over 2 days of constant operation

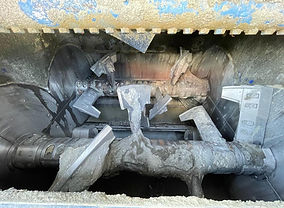


Current Solution
After mixing of cement, workers will carry out hacking process on hardened cement in the mixer, this is dangerous and can cause equipment to wear out faster.
As there is minimum down time due to production quota, this hacking process can only be carried out at the end of day or at the end of batch production.
The leftover cement will only continue to buildup with every single usage causing significant effort required to be removed
.jpg)

Our Solution
​
By integrating multiple high-pressure water nozzles, we can target the blades and shaft inside the mixer.
This jetting action helps dilute and rinse away any residual cement, leading to a cleaner and more efficient mixing process.
The integration of Water Jetting into cement mixers is straightforward. By installing strategically positioned high-pressure water nozzles within the mixer, we can achieve comprehensive coverage of all critical areas.
The water supply can be controlled to suit different cleaning and maintenance requirements.
High pressure system added to BHS cement mixer to reduce downtime due to maintenance processes. By installing a washing system;
- Reduced leftover cement will minimize cleanup efforts and increase overall cement mixing productivity.
- Decreased material waste translates into cost savings for your projects.
- A more efficient mixing process means smoother project execution and potential timeline improvements.
Revolutionizing Concrete Cleaning, One Plant at a Time
Foamwork Systems
Water jetting is a highly effective method for cleaning foamwork systems. By using high-pressure water streams, it can effectively remove dirt, debris, and other contaminants from foamwork surfaces without damaging the delicate materials.
This method is also eco-friendly as it does not require the use of harsh chemicals or solvents. Overall, water jetting is a reliable and effective cleaning solution for foamwork systems.
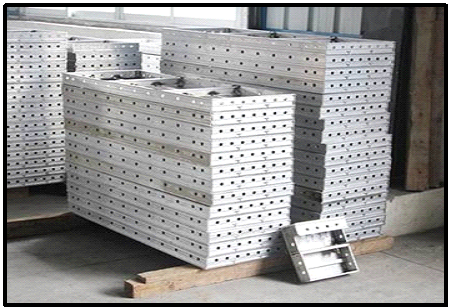
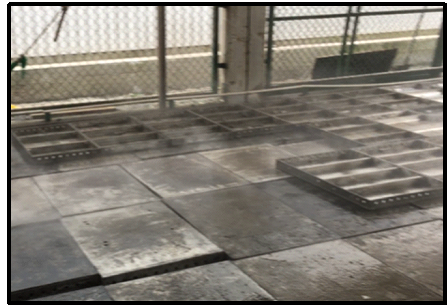
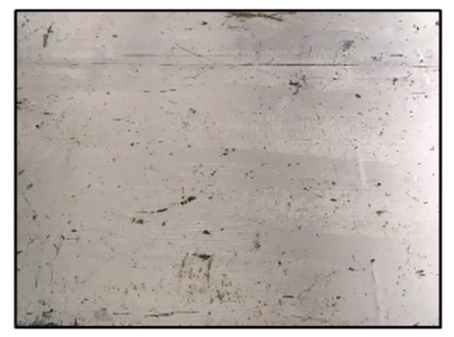
After Water Blasting
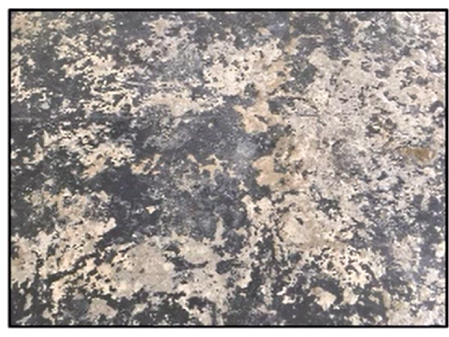
Scaffolding
Water jet cleaning is an effective method for cleaning scaffolding. The high-pressure water stream can easily remove dirt, debris, and other contaminants from the scaffolding surfaces without causing damage. Water jet cleaning can also help to remove rust and paint, leaving the scaffolding clean and ready for use.
It is an eco-friendly and efficient cleaning solution that does not require the use of harsh chemicals or solvents, making it a safer option for workers and the environment.
​



After Water Blasting

Scaffolding
​
Hardened cement takes up space on surfaces
Increased in weight of basic structures
​
CEMENT MIXER
​
Hardened cement takes up space/
volume in the cement mixer.
Volume of cement decreases each mix
due to previously harden cement.
Leading to more batches of cement
required for future mix.
​
CEMENT TRUCK
​
Cement residue on the truck creates
extra weight over prolonged usage.
More fuel required due to additional
weight on cement truck.
Increased fuel consumption will affect
operation cost and time required at refueling
stations.
Concrete Roughening
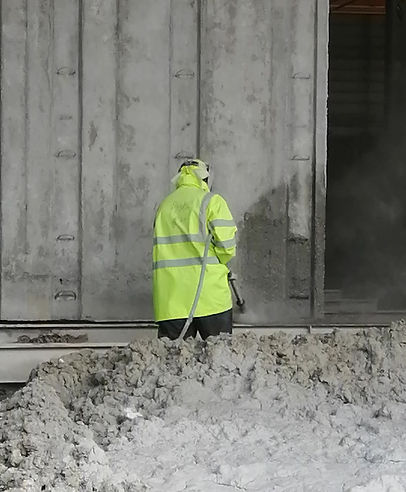
Concrete roughening is the process of creating a surface profile on a concrete substrate to enhance the adhesion of coatings, overlays, or other surface treatments.
Â
This can be achieved through various methods such as shot blasting, scarifying, grinding, or milling. Roughening is important because it provides a mechanical bond for the coatings or overlays, which helps prevent delamination or detachment.
Â
Additionally, it can improve slip resistance, which is especially important for high-traffic areas or outdoor surfaces.
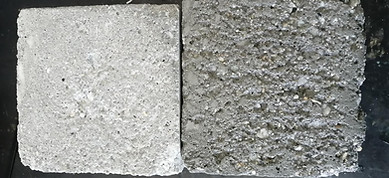
Recommended Products

UHP Water Jetting
Hammelmann
MAWP: up to 4500 bar
Flow rate: up to 50 l/min.
Diesel Model
Suitable for Concrete cutting with abrasive
Suitable for Surface Roughening
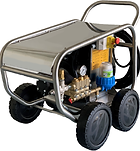
Electric Water Jetting
Marlin Series
MAWP: up to 500 bar
Flow rate: up to 17 l/min.
Suitable for Touch up

Electric Water Jetting
Marlin Series
MAWP: up to 1000 bar
Flow rate: up to 17 l/min.
Suitable for Loose Cement remover
Suitable for Surface Roughening
OFFSHORE
MARINE
CONSTRUCTION
CHEMICAL
bottom of page